Please note: All information is correct at time of publication. Our service is always evolving; if you're a current customer, please refer to your Driver Handbook for up-to-date policy information.
An unfortunate fact about switching to an all-electric car, is that they’re typically more expensive to buy or lease than an internal combustion (ICE) equivalent.
However, making the switch to an electric car is often far more affordable than most people think. Especially if you utilise a salary sacrifice scheme. This slashes the monthly cost down to a far more attractive price than purchasing outright or a traditional lease deal. Even with the electric premium and a rise in energy cost - electric cars are still cheaper to run than a traditional ICE vehicle.
So why are electric cars more expensive? We’ve identified three key factors:
- Batteries are very expensive
- Demand still far outstrips supply
- The leasing industry is still skittish about residual values for electric cars
Below we’ll have a look at the large upfront cost of the battery within an electric car, how supply chain issues are pushing prices up and why leasing companies still charge such a premium on electric cars.
That’s actually why loveelectric was created. We wanted to get as many people behind the wheel of an electric car as possible; with minimal fuss at the most affordable price point.
1) A battery for an electric car costs £5,600 on average
Batteries remain the chief reason that electric cars demand such a cost-premium. Even though the first iteration of an electric vehicle was created all the way back in the 1830s, the development of lithium-ion batteries has taken rather a long time to catch up.
Manufacturing processes are driving the price down, however a large proportion of the RRP of any electric car is to buy the battery pack within it.
Take the Tesla Model 3 for example; one of the most popular cars (electric or otherwise) on the market. A replacement battery from Tesla is £5,220 (as of July 2022). With a sticker price of £47,500, that’s nearly a tenth of the car’s entire value in just a single component.
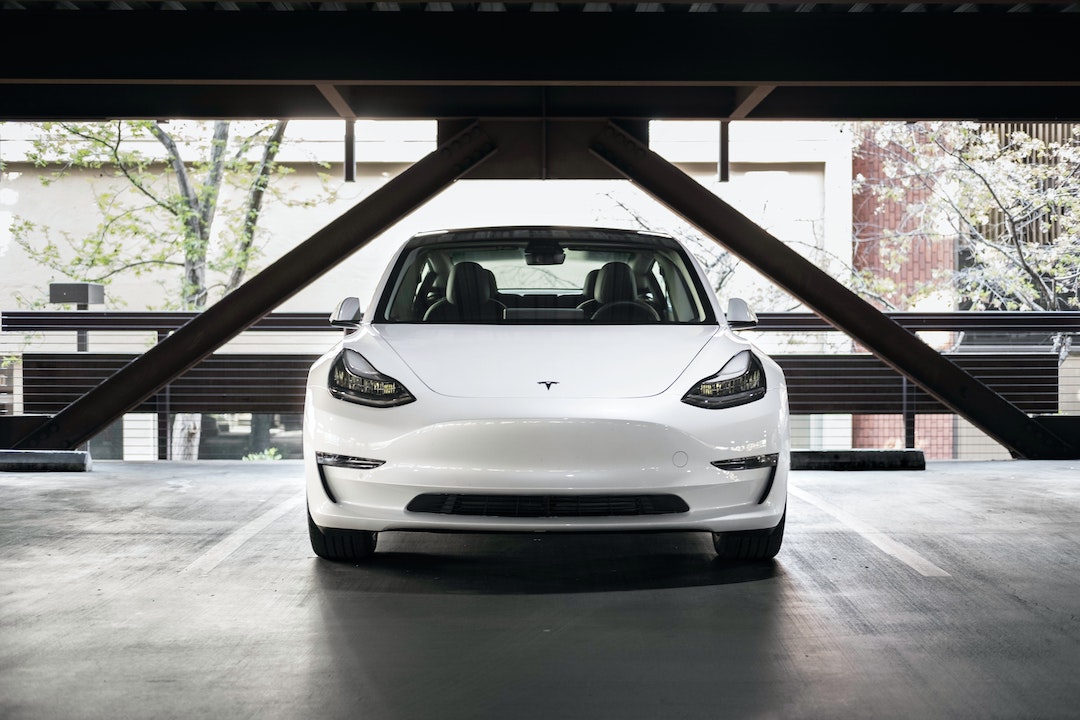
Why does the battery pack used in an electric car cost so much?
To begin with, the battery packs used by electric cars actually consist of hundreds of cells. To produce such a large lithium-ion pack requires lots of raw materials - some of which are precious metals and rare elements; cobalt, nickel and lithium to name a few.
Extracting cobalt and nickel from mines is a costly process, with lithium refinement requiring a large amount of water.
These processes are both costly and time intensive, however the below graph shows the rapidly declining cost of batteries over the past 30 years - dropping 97%.
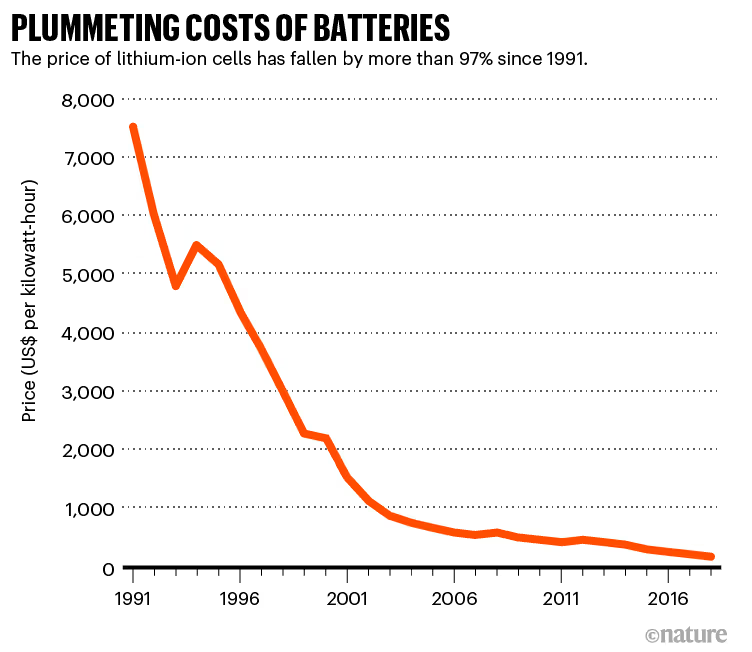
The dominance of lithium-ion cells is unlikely to change, so with further refinement and R&D - many experts predict that electric cars may actually reach price parity with their ICE counterparts by the mid-2020s.
Renault’s innovative workaround
Battery cost may be plummeting now, but during the early 2010s manufacturers with all-electric models were faced with a problem. The battery pack represented an even larger proportion of the vehicle cost than it does today.
Upon the introduction of the LEAF and Renault Zoe in 2011, the resistance to electric cars was still high. Negative media stories were frequent. Misleading headlines include “Electric cars ‘bad for environment” and “That blissfully quiet electric car might just kill you”.
The most concerning claim to consumers was that battery packs deteriorated quickly. Coupled with a higher overall cost than petrol or diesel cars and the prospect of an electric car was far less attractive than it is now.
Some added the premium onto the sticker price, but this made cars like the Nissan LEAF nearly £10,000 dearer than its closest ICE counterpart. Although back then, electric car grants were far more generous, bringing the real cost difference down to around £5,000.
But it still represented a significant dilemma for manufacturers. Lose money hand-over-fist in the hopes of starting an all-electric revolution, or push the cost of their vehicles up into an unattractive price bracket.
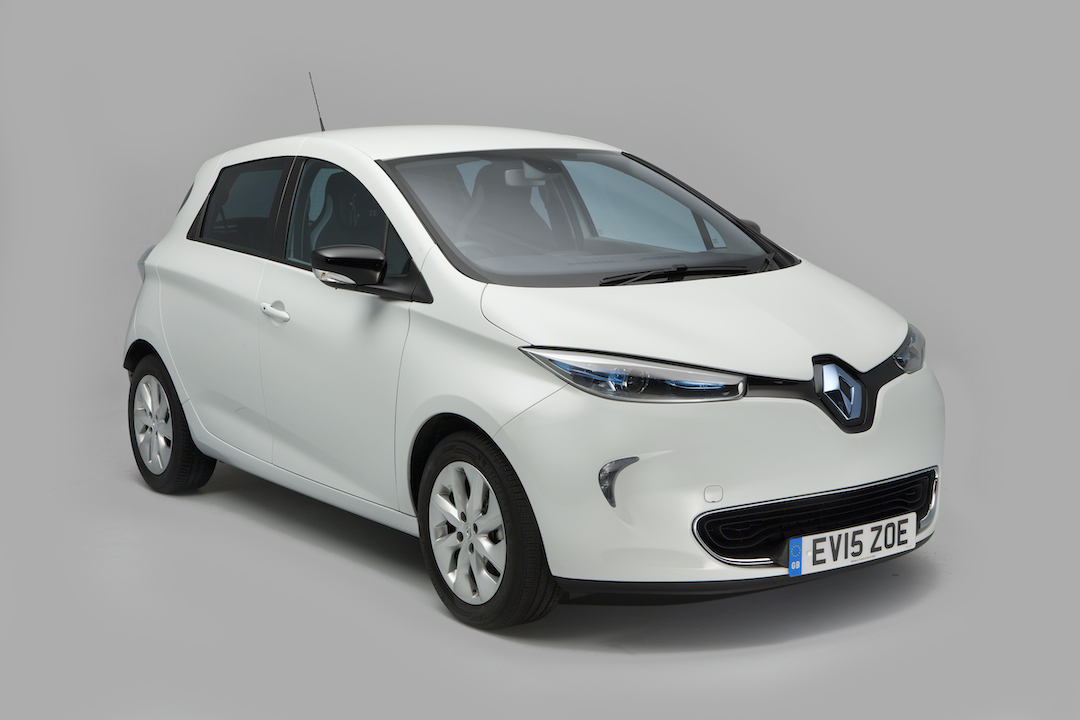
Renault introduced a third way: why not lease the battery?
From 2014, all-electric Renaults were available with two options: outright purchase, or own the vehicle but lease the battery that powered it.
There were a number of perks to leasing the battery:
- Battery health was guaranteed for the duration of the vehicle: when (if it ever did) efficiency dropped below 75%, the battery would be repaired or replaced for free
- 24/7 breakdown cover was provided as standard
- The lease was easily transferable to a new owner if the car was sold
This solution dramatically reduced the price of a vehicle by around £3,500 - £6,000 on the used market. It was an innovative solution and aided electric adoption for many.
However, in 2019 Renault decided to ditch the deal. This wasn’t due to lack of popularity or interest in electric cars - quite the opposite. With significantly improved residual values on their all-electric offerings, the French brand was able to offer a more competitive outright purchase price.
Family hatchbacks like the Renault Zoe are a great option for dipping your toe into the world of all-electric motoring; they’re affordable and still incredibly practical for daily driving. In fact, they can be leased via a salary sacrifice scheme for as little as a few hundred pounds a month!
Future of batteries
Huge strides are being made to advance battery technology and ramp up production.
Battery Tech
Demand for batteries with increased ranges has led companies like Britishvolt to invest huge sums of money in R&D facilities. Its Hams Hall site in the West Midlands will be a 260,000 sq. ft. behemoth dedicated solely to the further innovation of production-ready battery cells.
The goal is to drive the cost down by producing better performing cells on a bigger scale than currently available. This saving can then be passed onto the end user - aka. drivers - as manufacturers start paying less for their batteries.
Once these cells are production ready, they’ll be transferred over to Britishvolt’s partner gigafactory in Northumberland where they can be created in vast numbers.
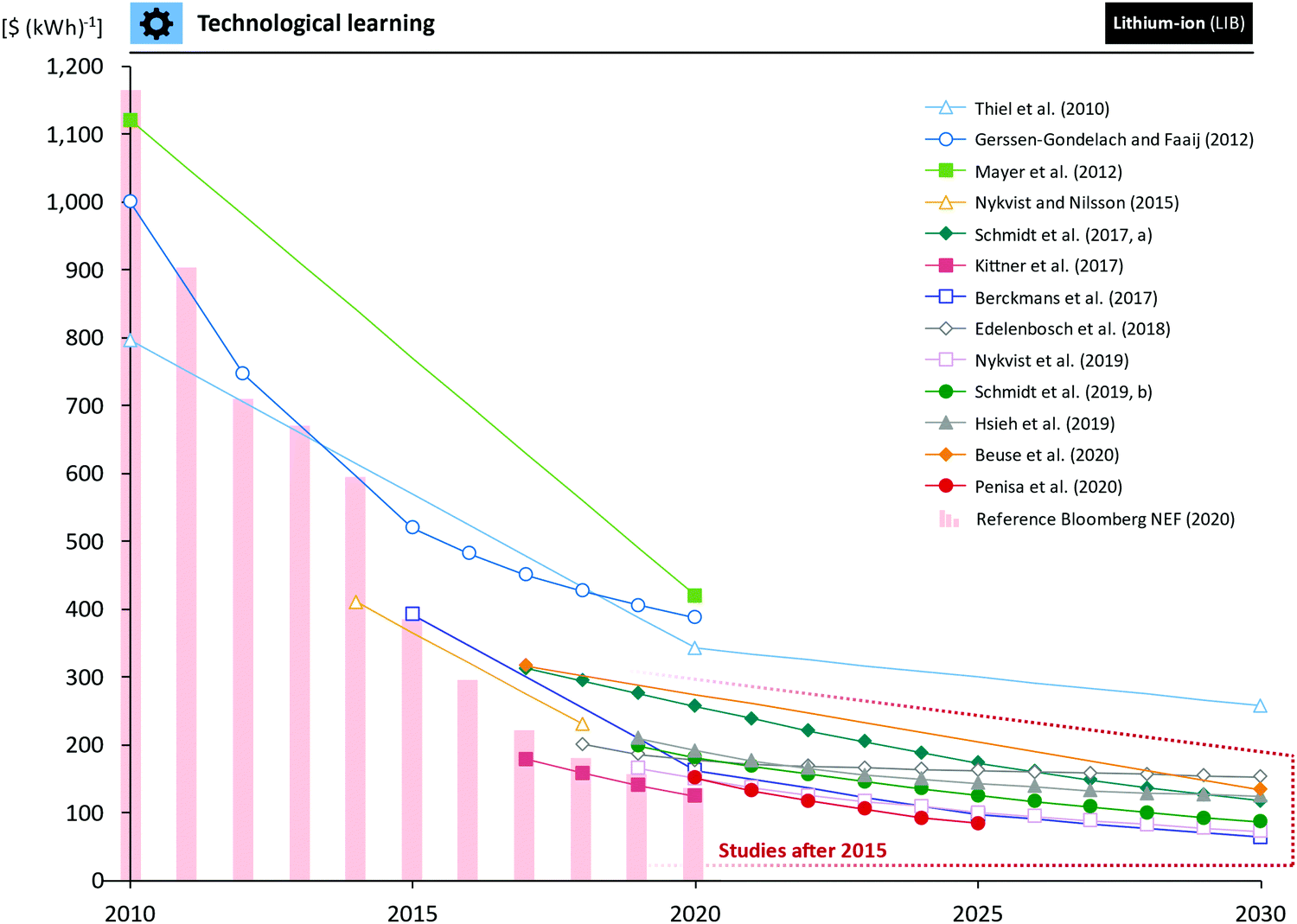
Production and Gigafactories
Gigafactories are becoming incredibly important for the mass adoption of electric cars. A gigafactory is a battery production factory and derives its name from a large unit of energy: the gigawatt (GW).
To put into perspective, 1 GW is equal to 1,000,000 x kilowatts (kW).
These factories are solely dedicated to producing enough battery packs to supply manufacturers. Ahead of the curve - as per usual - is Tesla. The OEM began to build a gigafactory out in the Nevada desert all the way back in 2014, with another two planned for Berlin and Texas.
Once opened, these gigafactories won’t be able to make packs fast enough. A forecast by Benchmark Mineral Intelligence has stated that Britain is going to need at least 175 GWh of battery capacity by the year 2035 to supply 3 million+ EVs.
There’s currently only three manufacturing plants planned for development in the UK. Using those, the UK’s output is due to reach a combined capacity of around 57 GWh by 2030. This may sound impressive. However it’s merely 5% of Europe’s total projected GWh capacity, compared to Germany’s enormous 34% of output.
It’s imperative that the UK secures investment in more gigafactories. When the ban on ICE vehicles comes into effect in 2030, there’ll be a need for around 100 GWh of supply - this is equivalent to five gigafactories producing 20 GWh of energy per annum.
So, batteries remain a large aspect of an electric car’s cost. As it currently stands, this cost is then passed onto the consumer, presenting a higher upfront cost compared to their petrol/diesel-powered equivalents.
But, battery tech is constantly evolving. Furthermore, electric cars do offer a significant reduction in running costs (lower maintenance, fuel vs. electricity) and generally work out far cheaper on a pence-per-mile basis. Even when taking into account the recent rise in energy cost, an electric car is still cheaper to run than a petrol/diesel equivalent.
What’s even better is opting to lease via a salary sacrifice scheme. This slashes the monthly cost of an electric car, there’s no deposit and everything is included in the per month figure you’re quoted! Even more reasons to loveelectric.
2) Supply and demand
If you build it, they will come. This misquoted line from an ‘80s film may have been used by inspirational Instagram accounts for years, but when it comes to electric cars it couldn’t be more apt.
The UK has officially embraced the electric car, with 1 million EVs already on the road. The problem is, the all-electric boom happened just as the globe’s supply chains were stopped dead in their tracks. This knock-on effect is still being felt by manufacturers around the world and directly impacts the cost of electric cars today.
Manufacturers can’t keep up with demand
In short, automakers simply can’t make vehicles fast enough.
This isn’t a problem just for electric cars, but all cars. All vehicles in fact. The rapid uptake in electric cars since 2019 coincided with one of the largest disruptions to contemporary society (outside of war) the globe had ever seen. The repercussions of that period are well documented and still being felt by the largest manufacturing industries today. Not least of all the automotive industry.
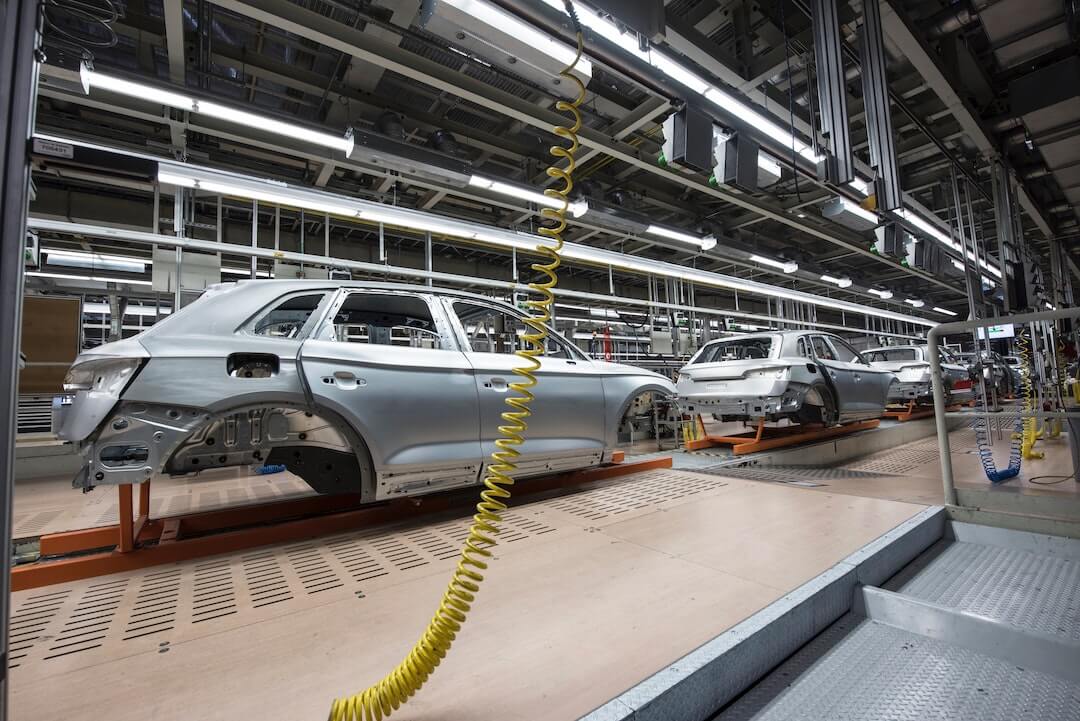
Semiconductor shortage
The most impactful aspect is the shortage of semiconductor chips. Electric cars are incredibly reliant on state-of-the-art technology that can not function without the chips. These semiconductors are vital for key features, such as; advanced driver-assistance systems and enhanced connectivity (Apple CarPlay, Android Auto etc.)
Exacerbating the problem is that it’s not just the automotive industry that’s reliant on these chips. Laptops, mobile phones and wireless communication all need semiconductors to function. With the seismic shift in working culture, working from home solutions skyrocketed - thus did the need for even more semiconductor chips.
Further putting the automotive industry on the backfoot is the manufacturing process for vehicles. Most OEMs deploy a “just in time” strategy; ordering semiconductors and key components just before production of the car begins. Historically, this was to keep inventory costs to a minimum. Demand for cars actually dropped in 2020, so manufacturers pared back their semiconductor orders.
But as demand swelled, automakers didn’t have enough semiconductor inventory to ramp up production. Furthermore, other industries that didn’t rely on the “just in time” manufacturing process had procured the extra semiconductors available after OEMs reduced their orders.
This shortage isn’t going away anytime soon, unfortunately. Experts predict that production of semiconductors won’t satisfy demand until 2024.
So - what does this mean for electric cars?
Well, if you’re looking to buy brand new - it probably means a prolonged period of higher lead times.
However, loveelectric has direct relationships with manufacturers and the largest leasing companies in the UK. That means exclusive access to stock before it goes public at a hugely discounted monthly price.
Used car market
With electric car leasing becoming a popular choice back in 2019, some of those vehicles are now coming to the end of their lease term and hitting the used market. Generally, this is good news.
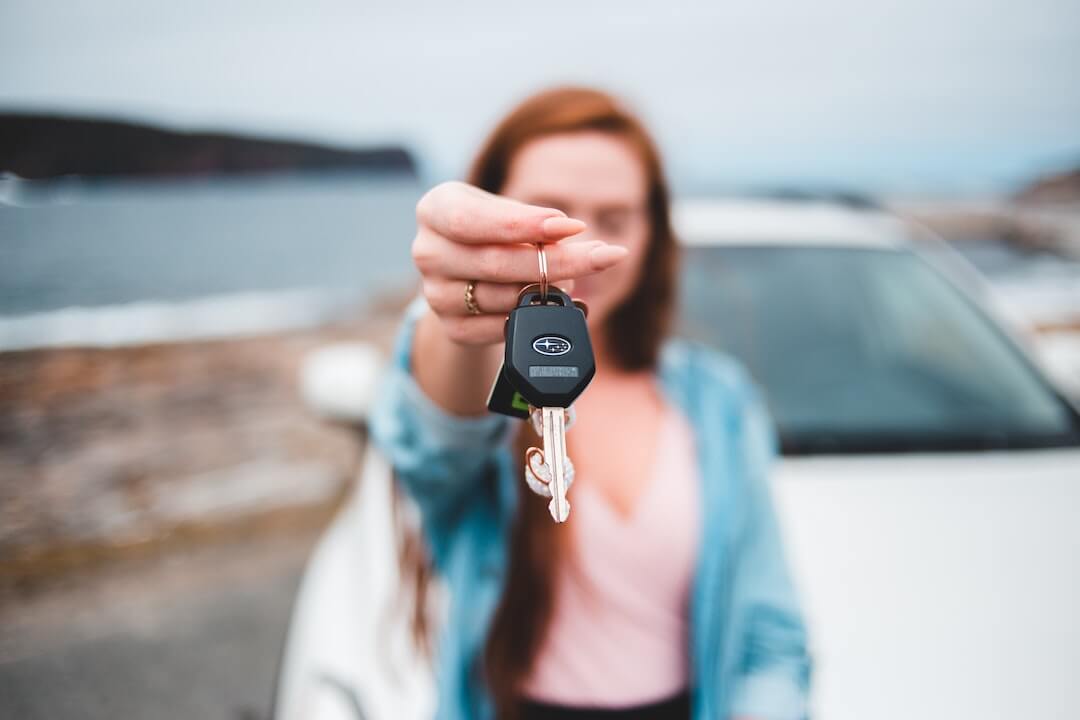
But demand for cars still far outstrips the available stock which puts pressure on the used market.
To understand why, let’s first look at the typical leasing journey of a brand new car.
- The manufacturer sells the car to a leasing company
- An individual or business then signs a lease agreement for 24/36/48 months
- Once that lease agreement comes to end, the individual/business will typically sign up for a new car and begin another 24/36/48 month contract
- The lease company will then de-fleet that stock into the used marketplace
With traditional petrol/diesel cars, the abundance of models allows this cycle to continue in perpetuity. The story is different with electric cars.
Businesses are increasingly concerned with their carbon footprint and improving green credibility. This results in many businesses moving away from typical company cars; German diesel saloons and switching to the Tesla Model 3.
With demand only increasing, leasing companies are unable to buy enough stock from manufacturers. The effect of this is twofold:
- Businesses and individuals alike, are simply extending/renewing their leasing contracts beyond the initially agreed term due to lead times.
- Instead of de-fleeting stock and putting it back into the used market, leasing companies are holding onto electric cars far longer than ICE equivalents.
This pent-up demand for electric cars may be problematic for used car buyers. There’s less stock and high demand, resulting in a price increase for all electric cars that do trickle into the used car market.
3) The leasing industry’s perspective on electric cars
As we’ve discussed, electric cars still demand a premium over their fossil-fuelled counterparts. If it’s more expensive to buy, it’s more expensive to lease - that’s simple economics.
However, it’s a bit more complicated than that.
The vast swathes of people making the switch to all-electric motoring has happened incredibly quickly. Unfortunately, the leasing industry isn’t structured in a way that’s able to respond to dramatic change in buying habits, which has driven the monthly lease cost upwards.
Let’s take a look at how leasing a car actually works and why the switch to electric cars has sent prices all over the place.
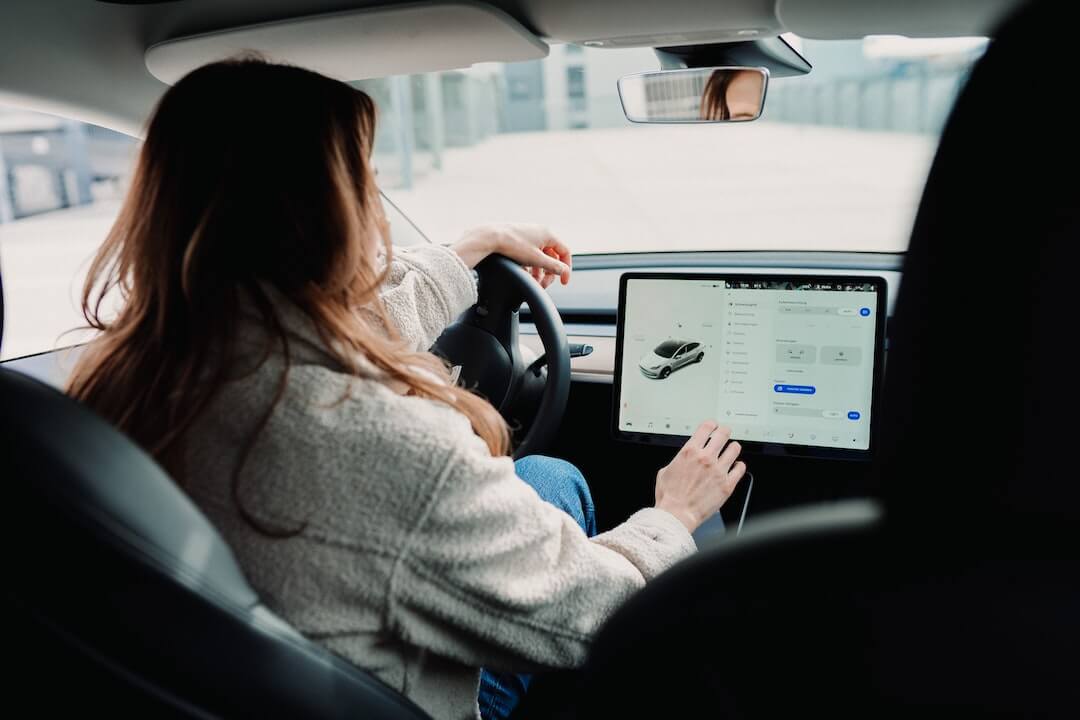
How leasing works
Before offering a monthly price to customers, a leasing company must first calculate the residual value of the vehicle. That is, how much the car will be worth at the end of the lease agreement.
This is the most important figure for any leasing financier; it’s the figure on which the entire lease agreement hangs from. Once the residual value is calculated, the underwriters work backwards from there and produce the monthly rates at which they can offer the car to customers.
There’s multiple factors that affect the residual value of a vehicle.
Key influences are typically mileage and the length of the lease term. This is why when you’re configuring a lease deal, these are the two leading information points after choosing the car.
- Mileage has a well-documented impact on the value of a vehicle; the general rule being the lower the mileage, the more valuable it is.
- The length of the lease of course dictates how outdated that particular model will be in 24, 36 or 48 months time. If a new iteration of that model is released during the lease term, by the end of the lease that model will have dropped in value.
In short, a lease is all about the risk to reduction of value.
A leasing company’s bottom line is protected by aversion to risk. This ensures profit without the potential of unnecessary fiscal loss. When it comes to salary sacrifice schemes, many providers will over-inflate their prices and pass that risk onto the employer - or purposefully obscure their pricing structure.
At loveelectric, we make our profit in a way that’s cost-neutral to the employer and fair to the employee. We also charge a small service fee which is covered by the employer's savings in National Insurance contributions - so the scheme always remains cost-neutral for the employer.
Why electric cars still cost more to lease
Electric cars are expensive to lease for two reasons:
- Batteries remain a disproportionately high percentage of an electric car’s value
- There aren’t enough electric cars on the used marketplace
As petrol and diesel cars have been a staple of personal transport for over a century, there’s an abundance of second-hand models filling the used marketplace. 99% of makes and models have a long lineage of previous iterations.
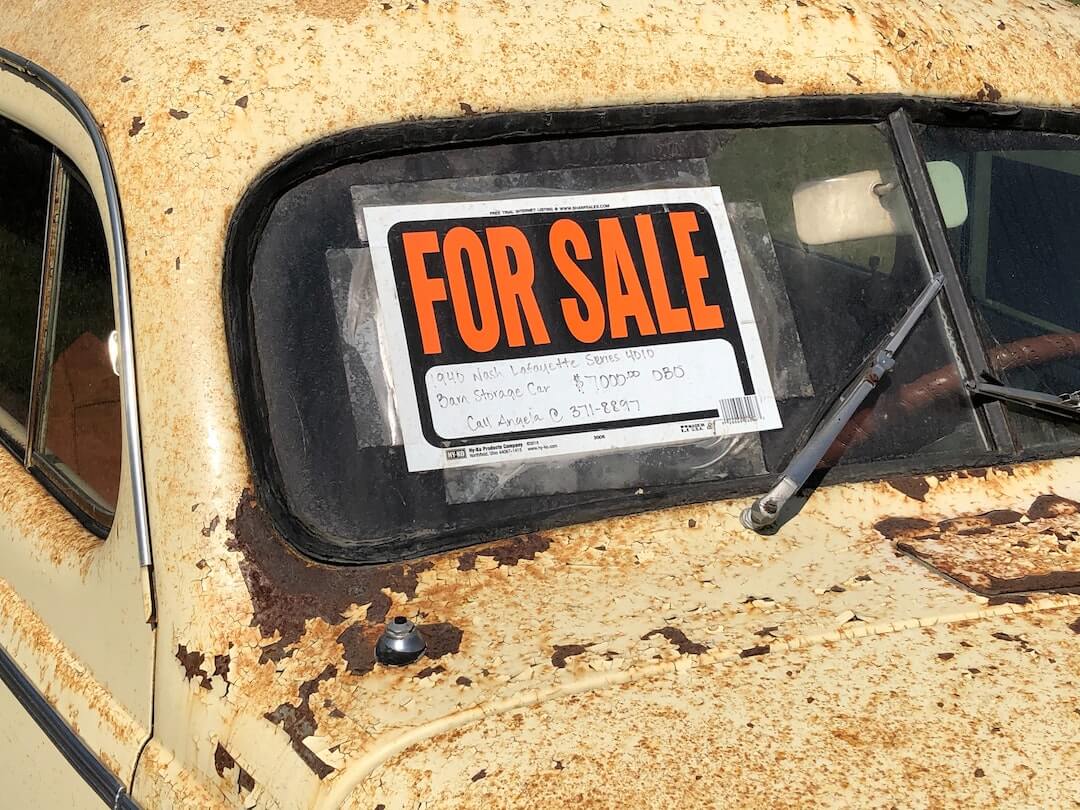
This vast amount of data makes it incredibly easy for financiers to reliably predict the residual value of an ICE vehicle; simply look at the used market and find the same model but 24/36/48 months old with a similar mileage.
Electric cars simply haven’t had time to proliferate the used car market yet. That makes it difficult for leasing companies to reliably predict how much an electric car will be worth in 2-4 years. To offset this risk, the monthly price of an electric car lease goes up.
Now, onto the battery.
As we’ve previously discussed, batteries are the largest financial asset within an electric car. When purchasing outright, a high percentage of the sticker price is to own the battery that sits beneath the floor panels.
Worries still remain within the financial sector around the degradation of battery packs used within electric cars. Again, this is simply due to a lack of en-masse data. There are plenty of examples that batteries suffer only minor degradation over time - a Tesla Model 3 covered 100,000 miles and lost only 10% of its capacity - which is an impressive figure.
Another factor is how quickly advances are being made to improve battery tech. When considering the leaps and bounds made over the past 3 years alone, it’s understandable why leasing companies may be skittish to assume a battery will remain as valuable 48 months later than the day it rolled off the production line.
As it currently stands, banks remain reluctant to drop leasing rates. But there is hope on the horizon. With more evidence proving batteries resist degradation and retain their value, residual prices should stay buoyant and reassure leasing companies.
Plus, leasing through a salary sacrifice reduces the monthly cost of an electric car by a huge margin. Don’t believe us? See how much you could save here.
The future of leasing an electric car
Mike Todd - head of VW’s financial services in the UK - suggests it’ll take around three to four years before there’s a drop in lease prices. This is to allow:
- Enough electric cars to hit the used market
- Battery degradation data to be more widely reported
- Residual values to cement rather than remain speculative
As discussed, electric cars hitting the used market are commanding high prices due to demand far outstripping supply. For many, this means that even purchasing an electric car second-hand will remain prohibitively high.
It may sound counterintuitive, but this is good news for leasing deals.
With less risk involved in leasing an electric car, financiers are able to drop the monthly cost to a competitive level - eventually bringing them in line with the current cost of ICE counterparts.
The BVRLA estimates 5 million vehicles on Britain’s roads are currently leased. With the impending 2030 ban of new ICE vehicles looming large for motorists and manufacturers alike, it’s an inevitability that leasing an electric car will become the most popular form of personal transportation.
By far the most affordable option, salary sacrifice slashes the monthly cost of an electric car lease compared with a traditional leasing deal. There’s no deposit and everything is included in the per month figure you’re quoted. Get in touch and find out all the reasons to loveelectric.
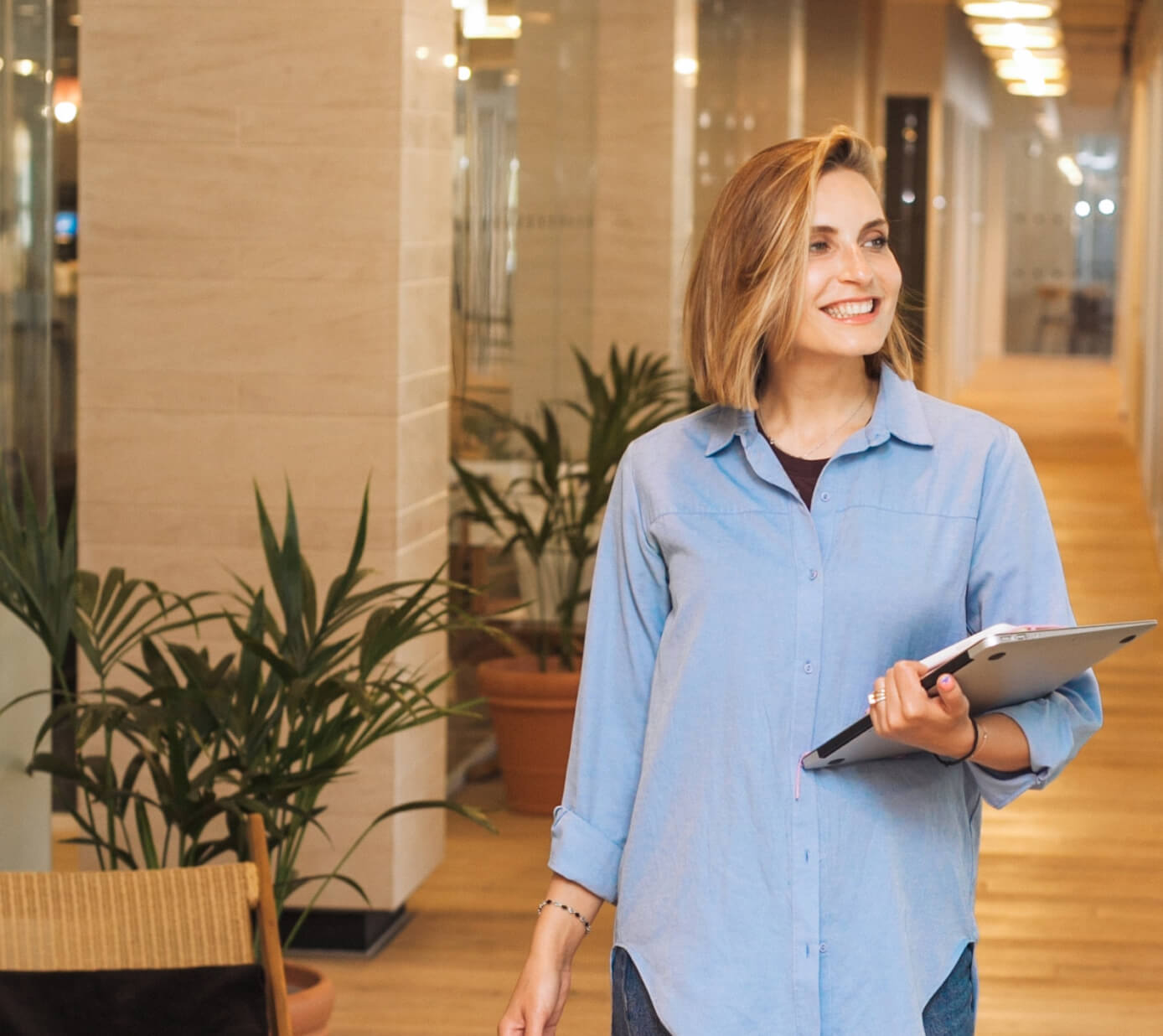